All You Need to Know About
Anti-Reflective Lenses
By Larry
Clarke
Issue Date: February
2004 |
Expiration Date:
February 28, 2007 |
This course is approved for
one (1) hour of continuing education credit by
the American Board of Opticianry (ABO).
Course # SWJP217-1 |
Learning
Objectives: |
Upon completion
of this program, the participant should be able
to: |
- Communicate to
patients and customers the importance of AR
lenses.
- Demonstrate the
typical AR application process.
- Explain why
refractive index is a key factor in defining the
need for AR.
|
| |
|
|
|
|
HOW DOES AR COATING WORK?
The
basic concept for how anti-reflective coatings work is
the optical interference model. Each coating layer in
the AR stack combines with previous layers to cancel out
a broad range of light waves by introducing opposite, or
destructive, waves that are out of phase. Thus,
reflective properties of that range of light are
neutralized. By applying the principle of optical
interference, we are able to increase light transmission
to nearly 99 percent in most cases. The result is a
reduction of reflections over a broad range of
wavelengths... and clear, crisp vision for your
patients.
DESTRUCTIVE INTERFERENCE MODEL
By
causing the reflection from the second surface to be
exactly 1/2 wave length out of phase from the reflection
from the first surface, an AR coating causes the two
reflections to cancel each other out, eliminating
reflection. Please note that in the interest of
simplicity, the destructive interference model used is
based on a single wave length of light entering a lens
at normal incident. In the case of a real lens coating,
the mathematical formula and models used to design an AR
coating are much more complex. (See illustration on
following page.)
STANDARD LENS WITHOUT AR
Standard, uncoated lenses can decrease light
transmission by up to 15 percent of available light.
This is caused by visible reflections on the front and
back surface of the lens, as well as internal
reflections. The higher refractive index of a lens
material equates to the greater incidence of reflections
and glare. (See illustration on following page.)
WHY DO SOME AR BRANDS REFLECT A DIFFERENT
COLOR THAN OTHERS?
When seen from an angle, all AR
lenses reflect a small amount of color/hue, typically
referred to as residual color. Some AR brands look
green, while others appear blue or yellow-green. This is
a natural phenomenon associated with the reflectance
curve of a broadband AR coating across the visible
spectrum of light. AR coatings have a peak reflectance
(approximately 1 percent) at some point on the visible
light spectrum and it is the color associated with that
peak, which is reflected more than other colors.
Most
AR producers choose their AR layer design and resulting
peak color reflection based on customer preference or
visual performance goals. The ability to help control
manufacturing consistency is also a major factor. Peak
reflectance tends to drift slightly from day to day,
affected by environmental changes in production such as
vacuum chamber cleanliness or even changes in humidity.
Many AR coatings tend to have peak reflectance in the
520 to 550nm range of the light spectrum, the green area
of visible light that also tends to be the easiest color
to produce consistently. Some manufacturers move the
curve peak closer to the blue end of the spectrum, while
others move the peak toward the yellow.
Visual performance such as eye sensitivity during
daytime or twilight has also been cited as criteria for
residual color choice. It is, however, difficult to find
credible evidence or studies on this subject that will
make the choice an obvious one. Feel free to ask your
supplier how they chose their peak reflectance color.
IS IT POSSIBLE TO HAVE A COMPLETELY CLEAR
AR?
Theoretically, yes it is possible... but this
requires a very complicated and tricky AR stack design
that is nearly impossible to consistently maintain in a
real production environment. In addition, some companies
that attempted to market a near-clear or flesh-toned AR
experienced resistance. Upon receiving their new
eyewear, consumers sometimes expressed buyer's remorse
when they were not able to easily recognize a visual
difference from a normal clear lens.
AR Coated Lens |
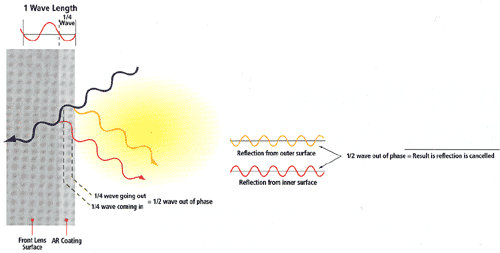 |
Destructive Interference
Model By
causing the reflection from the second surface
to be exactly 1/2 wave length out of phase from
the reflection from the first surface, an AR
coating causes the two reflections to cancel
each other out, eliminating reflection.
| |
SHOULD THE REFRACTIVE INDEX OF AR MATCH
THE REFRACTIVE INDEX OF THE ACCOMPANYING LENS
MATERIAL?
Light Transmission= Clear, Crisp
Vision |
Lens
Material |
Index |
Without AR |
Including Multi-Layer
AR |
CR-39 |
1.50 |
92.06 |
99.1 |
Glass |
1.52 |
91.04 |
99.2 |
Polycarbonate |
1.59 |
89.4 |
99.2 |
High-Index Plastic |
1.60 |
89.4 |
99.0 |
Super High-Index Plastic |
1.67 |
87.8 |
98.2 | | Recently a
number of AR manufacturers advertised that they have
matched the refractive index of their AR to that of a
particular high- index lens material. The question
arises, does this combination create a benefit?
According to the science of thin film design, AR coating
should match the refractive index of the hardcoat,
not the lens material. The question then becomes:
when the indices of AR and hardcoat match, is there a
benefit? The answer to this question is still not
simple. For instance, if the AR and hardcoat refractive
indices match, but the hardcoat and lens material
indices are not in harmony, any benefit derived from the
AR/hardcoat match would immediately be offset. Whenever
there is a mismatch between the refractive index of lens
material and hardcoat, the result is what is
traditionally referred to as birefringence, the rainbow
effect often seen when a lens is viewed from the side.
AR coatings will never hide this effect. Having said all
this, it is important to note that a slight advantage
does exist when the refractive index of all three
components is in harmony--lens material, hardcoat and AR
coating.
Normal CR-39
Lens |
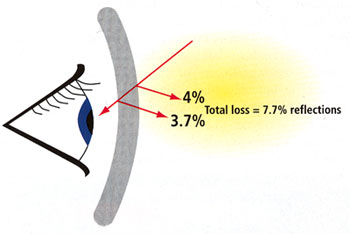 |
Standard Lens Without
AR Standard, uncoated lenses can decrease
light transmission by up to 15% of available
light. This is caused by visible reflections on
the front and back surface of the lens, as well
as internal reflections. The higher the
refractive index of lens material, the greater
incidence of reflections and glare.
| | In reality,
most hardcoats have a refractive index of approximately
1.5; the highest index for a hardcoat currently used in
our industry is 1.65. A common practice among AR
producers is to batch lenses from numerous manufacturers
with varying inherent hardcoat indices in the same
coating run. This forces the AR coater to choose an AR
index that matches most hardcoats, typically around 1.5.
In a perfect world, AR producers would have the ability
to coat all "like" lenses in each batch, where the
indices of the lens material and hardcoat are a perfect
match. Other than product produced by lens manufacturers
(commonly referred to as stock lenses), there are very
few AR producers who generate enough volume to justify
this degree of segregation. And even though there are
some minor cosmetic and visual advantages to a total
index matching system, the question is whether or not
the typical consumer can see the difference; and if so,
is it of value to them? Consumers to the ophthalmic
industry tend to place greater value on attributes such
as durability and lens thickness, as compared to other
lens features.
THE NEED FOR AR
Refractive index of a lens material is a key
factor in defining the need for AR. As evidenced by the
following table, the higher the index of a lens, the
more reflective it is; therefore, to achieve maximum
light transmission and resulting wearer comfort, it is
easy to see that AR benefits all lens products but
becomes even more critical on high-index lenses.
HOW IS AR APPLIED?
The
anti-reflective process takes place in a specially
designed coating lab, through a series of steps taking
anywhere from four to 10 hours. A truly effective AR
process incorporates the entire laboratory--from
surfacing to coating to finishing. It must begin in the
most pristine of conditions to be successful. The
environment must be clean and dust-free with a positive
air-flow. After lenses are cleaned, they are placed
inside of a vacuum chamber and microscopically thin
layers of low, medium and high-index materials are
alternately applied in succession to both the front and
back lens surfaces. Computer technology controls the
process with extreme precision so that each layer is
accurately applied. The following six steps demonstrate
a typical AR application process. To better understand
the precision with which this process must take place,
let's put it into perspective: the thickness of an AR
coating is equivalent to 1/5,000th width of a human
hair.
1 - Hardcoating After casting or
surfacing, an important step is for all lenses to
receive a scratch-resistant hardcoat prior to AR
coating. The hardcoat can be applied using a thermally
cured dipcoating system or via a process as simple as
UV-cured spincoating.
2 - Hand Cleaning Lenses are
individually hand cleaned to remove any remaining ink
markings, dirt and debris.
3 - Ultrasonic Cleaning Lenses
travel robotically through a cleansing process,
alternating between tanks of detergent, tap water and
deionized water.
4 - Degassing Lenses are baked
in a degas oven to remove all internal moisture and
provide optimal conditions for successful AR coating
application. The lens substrate determines oven
temperatures, varying from 50C to 75C, as well as
processing time, varying accordingly from one to four
hours.
5 - Inspection Hand inspection
assures optimal surface preparation prior to the AR
process.
6 - Vacuum Coating Lenses are
loaded into a rotating dome and various low, medium and
high-index inorganic chemicals are loaded into the
electron beam gun. The chamber is sealed and vacuum
pumps establish the prescribed vacuum pressure. Various
low, medium and high-index chemical layers are
evaporated from the electron beam gun at approximately
2000C and are deposited, one layer at a time, until the
AR stack is complete. Finally, the hydrophobic
top-coating is applied. The total process takes
approximately 90 minutes. Lenses are then removed,
inspected and forwarded to the lab finishing department.
WHY DO AR LENSES GET DIRTIER THAN NORMAL
LENSES?
They
don't. With normal lenses, reflections tend to hide the
dirt whereas with AR lenses, because they are so much
clearer, it is easier to see the dirt. It is like an
early detection system. A patient with normal lenses
will typically walk around for a day or more at a time
with dirty glasses that affect their sight due to
diminished transmission or light dispersion caused by
dirt that they don't notice. With AR lenses, the dirt is
noticeable and causes the patient to clean their lenses
more often resulting in better and safer vision. And,
although the earlier generations of AR lenses were
difficult to clean, the newest generations are far
easier to care for than ever before.
WHAT IS THE BEST WAY TO CARE FOR AR
LENSES?
Recommend a regular lens cleaning regimen,
complete with easy-to-use AR specific products that fit
the active lifestyles of your patients. Ask your AR
provider about what lens cleaning products they
currently have available:
- Lens spray cleaner, specially designed for
anti-reflective lenses
- Microfiber lens cleaning cloth
- Pre-moistened, disposable lens cleaning
cloths... great for travel and everyday use
Be
careful about recommending household cleaners. When
instructed by a dispenser to use a certain brand of
household dishwashing soap, some patients interpret this
to mean "any household soap." Unfortunately, some
caustic soaps contain ammonia, which will harm AR.
Patients will typically experience the best results when
using cleaners specifically designed for AR lenses.
ADVANCEMENTS IN HYDROPHOBIC TOPCOATING
Hydrophobic topcoating is a thin, organic,
polymer seal applied as the final layer of an AR coating
stack. Numerous new polymers have been introduced during
the past several years that substantially increase the
chemical resistance, repellency, abrasion-resistance and
ease of cleaning. The end result is an added patient
benefit as most AR coatings produced today are as easy
to clean as normal lenses.
WHY ARE TODAY'S AR LENSES BETTER?
During the past 10 years, most issues associated
with AR adhesion have been solved and AR developers have
turned their attention toward increasing abrasion
resistance. Numerous new brands have been introduced
during the past three years that boast of two- to
three-fold increases in scratch-resistance. Increased
hardness is achieved through the application of
specially designed hardcoat prior to AR coating with a
traditional AR stack or through the introduction of new
generation harder AR stacks on top of traditional
hardcoat. All of these new methods and brands result in
superior quality AR and are contributing to the
increased growth rate of anti-reflective lenses.
QUALITY CONTROL AND UNDERSTANDING
PLASTICS
Ten
years ago, most hardcoats were designed strictly for
hardness or tintability and AR compatibility was not
considered. Fortunately, this has changed dramatically
and most hardcoats, especially UV cured backside spin
coatings, are now being developed with AR compatibility
as the overriding performance criteria. In addition,
most AR coatings 10 years ago were applied by custom
coating houses that had nothing to do with the
manufacturing or surfacing of a lens. In many cases,
custom coating houses had no control over the lens or
hardcoat brands sent to them, nor in the surfacing
practices used on the lenses prior to AR coating.
Without knowledge of these factors, custom coating
facilities faced a situation where they had to treat all
lenses the same and therefore had to compromise quality
practices. Today, on the other hand, most AR coatings
are applied in or next to the same lab that manufactured
and/or surfaced the lenses; this adds a great amount of
control over the ultimate quality an AR lab can achieve.
Labs can choose the best hardcoat brands and can also
optimize their surfacing practices, back-side coating
practices and actual AR process to achieve the best
quality final product.
Dispensing Tips |
START IN THE EXAM
ROOM Patients put a lot of value on their
doctor's advice, so why not steer them toward
something that will give them an additional
visual and cosmetic benefit? When describing
your patient's new prescriptions and associated
lens recommendations, remember to recommend AR
lenses and tell your patient why.
|
WEAR AR
YOURSELF Everyone on staff who wears eyewear
should wear AR lenses. How will your patients
have faith in the product if their own optician
or doctor doesn't wear it? Personal testimonials
about why a staff member loves wearing AR lenses
can carry a lot of weight. |
DISPLAY AND
DEMONSTRATE Patients can feel bogged down and
confused by a lot of technical explanations,
especially if they are also hearing about new
lens materials and designs. A display showing an
uncoated and an AR-coated lens side-by-side is a
simple, effective explanation. Ask the patient,
"Would you rather your lenses look like this or
like this?" Many lens manufacturers, coaters and
laboratories supply comparison displays to their
customers. |
STAFF
EDUCATION A
well-informed staff is an effective, helpful
staff. Excellent training tools are available
from many manufacturers to keep your staff
well-versed on the subject. Hold role-playing
exercises in which staffers educate "patients"
on the benefits of AR lenses.
|
WHO BENEFITS FROM AR
LENSES Every
patient can benefit from more light to the eye.
And every patient should be given that
opportunity. Remember to discuss:
|
FUNCTIONAL
BENEFITS •
Night drivers •
Computer users •
Sunglass wearers •
Sports participants •
People who work in visually demanding
occupations such as police officers,
firefighters and pilots
|
COSMETIC
BENEFITS •
People see you, not your lenses
•
Attention focuses on your eyes, not the
distracting glare •
AR on
photochromic lenses makes them look clearer
indoors and eliminates the
glare that can occur in the darkened state
| |
|